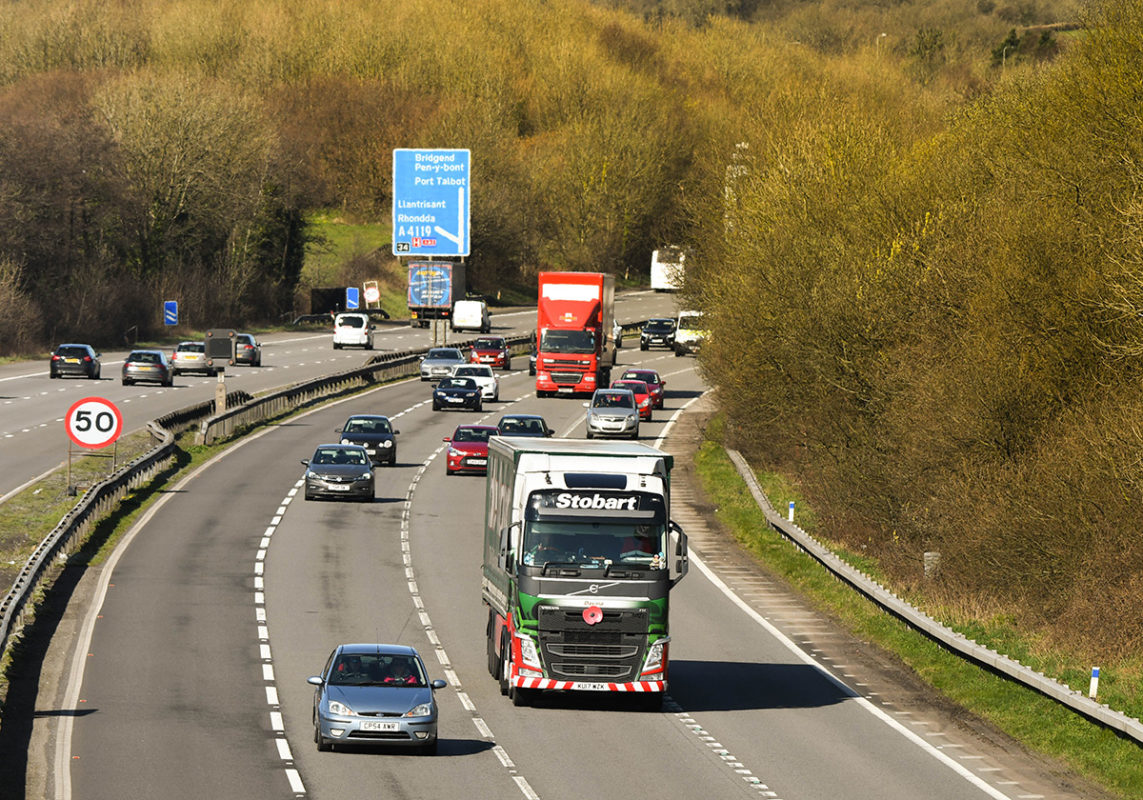
How Warehouses Have Changed in the Wake of Covid-19
Supply chains have felt the brunt of Covid-19. Most of the focus has been on the transport industry and its difficulties moving products domestically and abroad, however the warehousing sector has not been immune from challenges.
Increased volatility and unpredictability across all supply chains has been driven by erratic consumer behaviour. This has meant that some product lines have seen extraordinary demand, whereas others have experienced collapse. Cargo that was previously in high demand has been left to pile up in warehouses around the globe.
This has only been exacerbated by the rapidity that coronavirus gripped global locations. For instance, in late February and early March demand for Chinese products in the West was still strong. In the wake of global panic and eventual lockdown, demand disappeared overnight. This has resulted in a surplus of warehouse inventory.
Despite rumblings that the initial severity of the coronavirus crisis is beginning to abate, it’s overall impact on the warehousing sector will be anything but fleeting. We are still dealing with the effects of Covid-19, with some geographically specific regions having to implement lockdown again after initially lifting it. It’s clear that a structural transformation in how warehouses manage their inventory will be required.
Interested in learning how warehouses have changed in the wake of Covid-19? Keep reading to find out more.
Increased Inventory Holdings
Arguably, the most important trend to emerge is that of increased inventory holdings. Warehousing creates a bulge in the supply chain because inventories peak and trough depending on consumer demand.
The more uncertain the marketplace or economic environment is, the greater the need for warehouses to store goods and have an efficient despatch infrastructure. In the future, we’re likely to see more safety stock. Any economic downturn will mean less volume in the short-term, but the metric of inventory to economic activity will rise as the economy begins to recover.
As inventory rises, the more warehousing facilities will be required to store goods. Larger warehouses or more locations may be needed. However, the form this will take will depend on individual sectors the relationships between market dynamics.
Staffing and Third-Party Logistics
Following the economic downturn, retailers and manufacturers are more likely to regard large numbers of warehouse staff as a commercial liability, not an asset. Indeed, many employers believe that outsourcing manpower third-party logistics providers is a safer route to take as they navigate the economic fallout of the coronavirus.
Third-party logistics often have existing networks of facilities in multiple geographic locations. As downstream distribution networks (retailers) remain uncertain, the importance of utilising local marketplaces cannot be overstated, and will lead to retailers relying on logistics providers to do this for them.
Short-Term Logistics Contracts
There’s likely to be a move from longer to shorter-term logistics contracts. One of the challenges faced by warehousing during a volatile marketplace is that capacity is often secured on a short-medium term basis. Some contracts are longer – up to 10 years, but short-medium-term logistics contracts are likely to become the new norm.
Consumer goods, for instance, have historically faced a consistently year-on-year demand for logistics services. Covid-19 has changed this drastically, leaving companies exposed to having too much or too little inventory and warehousing capacity in the wrong markets.
Low Inventory Compared to Product Availability
The world’s largest retailer, Amazon, has fundamentally altered consumer behaviour – something that is influencing not just e-commerce but the whole of the retail sector. For instance, Walmart, a US retail powerhouse, is adapting their service offerings to match Amazon’s ability to deliver in noticeably short timescales. This may benefit the consumer, but it places added pressure on warehouse inventory levels.
Lockdown prompted a swell in product availability. Though this is not a direct consequence of Covid-19, some products have seen a dramatic rise in consumer demand. When combined with the customer expectations that businesses like Amazon and Walmart helped to cultivate, product availability becomes an issue.
If retailers are to match the service provided by e-retail platforms, they will need to create strategies that either increase in-store stock levels to continue to make home deliveries or develop a network of smaller, local warehouse facilities.
The Growth of On-Demand Warehouse Facilities
Covid-19 has presented the opportunity for so-called ‘on-demand’ warehouse facilities. These niche spatial solutions are proving to be quite popular with consumers, especially those with bespoke requirements.
It’s not unreasonable to assume that manufacturers and retailers will turn to these solutions to cope with the peaks and troughs of warehouse inventory requirements. A flexible approach may be the best way that warehousing can navigate the current health and economic environment.
Businesses may be hesitant to commit to long term warehouse leases which do not meet present needs. Many of these companies also offer ‘virtual warehousing’ which offers real-time global visibility for logistics assets, including inventory and vehicles. This allows inventory to be stored anywhere in the world, provided it can be distributed on an ‘as needed’ basis.
Enhanced Automation
Globally, sectors were already increasingly adopting automation. Covid-19 will only increase this emphasis – and warehousing is no different to any other sector. Expect adoption to increase in the foreseeable future.
This is further cemented by the low cost of borrowing and government incentives for making capital purchases which creates an attractive return on any business investment. Conversely, short-term unemployment levels and the migration of manpower from the high street to the logistics sector will make labour cheap and abundant. However, in the long-term mass automation adoption is inevitable.
This will likely have implications for the type and design of warehouses. Today, few have the infrastructure to accommodate automation and a large-scale evolution of layout and design will be needed. Vital investment will be needed before any one warehouse can run autonomously.
Focus on Green Warehousing
Following the Covid-19 crisis, many industry experts across a plethora of sectors have suggested that there will be a renewed focus on sustainability. The drop in emissions will encourage environmental lobbying and it has been suggested that the UK government, and other governments around the world – especially the US, will create policies that prevent (or at the least drastically reduce) pollutions levels.
Most of these policies will be aimed at transport and logistics which will affect supply chains. It’s been mooted that diesel will be banned in urban areas and this will make it difficult for goods to be brought to market from regional or national logistics facilities.
Any new buildings will be expected to conform to stern environmental restrictions and energy standards in addition to adopting green energy practices, such as installing LED lighting.
What the Future Holds
Coronavirus may overturn many of the key supply chain trends of the past three decades, but it certainly will not change any of the existing practices, such as low inventory. It will mean that companies will take a much multi-faceted approach to how they operate.
Low inventory is a shrewd (and most would argue) essential commercial practice in warehousing because it insulates businesses against the financial implications something like the coronavirus. The more money businesses have invested in inventory, the less can be invested in other areas of the business, like new product development or automation.
It’s likely that manufacturers and retailers will review the function of warehousing within their business models. Outsourcing and on-demand warehousing are likely to become highly viable solutions in the future, especially if the uncertainty surrounding coronavirus persists.
Green warehousing which focuses on environmental sustainability and policies designed to protect the environment will also affect how warehouses operate and look in the coming months and years. Though this may not be immediate, as the 2020’s unfold expect more and more warehouses to adopt a green ethos and processes.
Lastly, investment in automation will increase as warehouse companies strive to improve the resilience and efficiency of their operations. Robotics and materials handling look destined to be the most obvious automation examples, but the potential for automation to impact almost every area of warehousing cannot be ignored.
Warehouses Have Changed
It’s clear that warehouses have had to evolve to meet the demands of a changing commercial marketplace. Covid-19 has forced many businesses to adjust their business models to meet merchant and consumer needs.
From increased inventory holdings and short-term logistics contracts to utilising the latest technological innovation and placing a focus on greener solutions and sustainability, Covid-19 presents businesses with opportunities.
Estimating the length of time that Covid-19 will affect commercial enterprise is challenging. However, with sound planning and the implementation of an adjusted commercial strategy, businesses can insulate themselves from the more serious effects and emerge in a strong position, regardless of sector.
Chase News
Before and After: A Closer Look at Modular Dock Transformations
When it comes to improving logistics efficiency, the installation of modular dock levellers is one of the most effective upgrades…
Read More
Why Scissor Lifts Are a Game Changer for Your Business
If your operations involve frequent lifting, loading, or precise height access, a scissor lift could be the ideal solution to…
Read More
Maximising Efficiency with Installed Loading Dock Equipment
For businesses that handle goods loading and unloading, having the right loading dock equipment is essential. Installed products such as…
Read More